Quality Gates
Prevent Defects Before They Impact Production
Sigma Services partners with OEMs and Tier 1 suppliers to design, implement, and manage critical quality gates — ensuring defects are detected early, production lines stay protected, and customer satisfaction remains high.
From incoming material control to in-process validation and pre-shipment inspections, we install tailored checkpoints where they matter most. Our quality gates are backed by experienced inspectors, data-driven methods, and real-time visibility — giving your team the tools and confidence to stop issues before they escalate.
Why Quality Gates Matter
Every missed defect has a cost — in rework, downtime, warranty exposure, and brand reputation. Quality gates help you:
Catch defects before the point of install
Reduce line disruptions and contain supplier risk
Ensure compliance with customer or OEM requirements
Improve supplier accountability and process transparency
What We Do
Our team brings the tools, expertise, and systems to make your gates perform:
-
We design inspection gates specific to your parts, failure modes, and escalation paths — not cookie-cutter checklists.
-
Certified inspectors install and run gates at supplier facilities or OEM lines, ensuring process adherence and proper material handling.
-
Our quality gates are powered by Sigma’s suite of digital tools:
Custom Dashboards – Live defect tracking, inspection KPIs, audit trails
AI-Powered Automation – Predictive insights and decision support
Managed Quality Services – 24/7 monitoring, KPI optimization, monthly reporting
-
Issues are flagged and reported immediately. We handle dispositioning, segregate material, and support root cause analysis with your team or supplier.
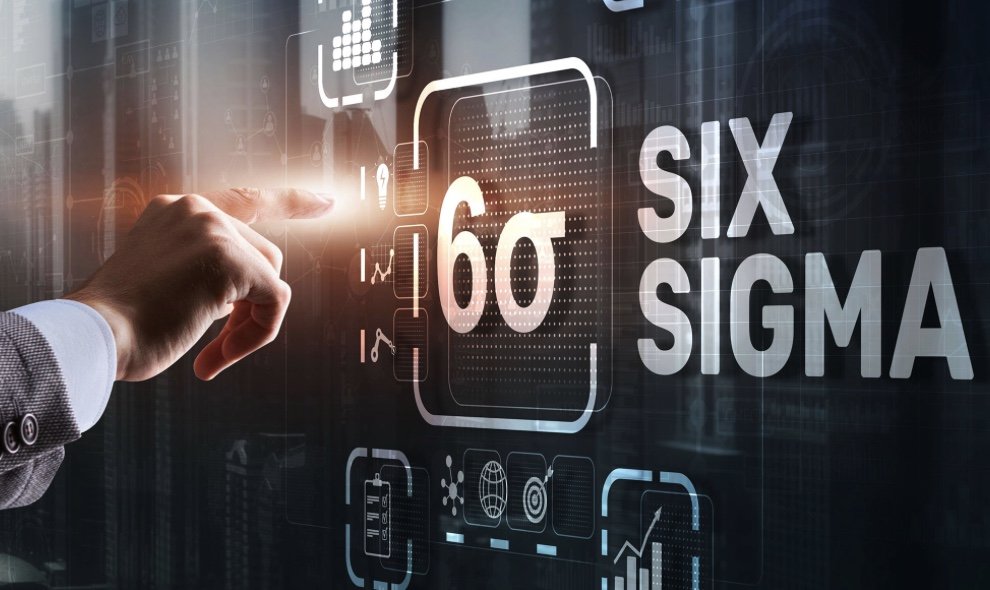
“Quality is never an accident; it is always the result of high intention, sincere effort, intelligent direction and skillful execution.”