Custom Dashboards & Digital Tools
Transform Data into Real-Time Quality Intelligence
Sigma Services builds custom digital tools that turn inspection activity into actionable insight. From mobile data capture to real-time dashboards and ERP integration, our systems are designed to give you full visibility and control over your quality performance — without the overhead of building your own infrastructure.
Whether you're managing a supplier network, running in-house quality gates, or trying to improve operational transparency, our tools put the right data in the right hands — fast.
The Sigma Advantage
Built by quality engineers, not just software developers
Seamless integration with Sigma field services and inspection teams
Custom-built, not off-the-shelf
Designed to scale across plants, suppliers, and customers
Optional AI and analytics add-ons for predictive quality insights
What We Build
Whether you need real-time dashboards, workflow automation, or full digital quality system integration — Sigma has the solution:
-
Custom-built dashboards give your team instant visibility into:
Defect types, rates, and trends
Inspection volumes by site, supplier, or shift
Containment status and escalation alerts
Operator performance and process adherence
Each dashboard is configured to match your internal KPIs, reporting formats, and escalation thresholds — so you see what matters most.
-
Our mobile interface allows your team to capture quality data from the floor or the field — including:
Part type and condition
Defect description and failure mode
Inspection method used
Containment or rework actions taken
Data is automatically fed into your dashboard, making reporting effortless and accurate.
-
We connect our tools to your systems — not the other way around.
With ERP and MES integration options, your inspection data can tie directly to:Inventory dispositioning
Supplier scorecards
Warranty tracking
Cost of quality reporting
NCR or CAPA workflows
-
Sigma’s platform uses AI to analyze historical inspection data and recommend optimized rework or inspection methods for similar parts or failure modes. These recommendations are reviewed by our engineers before being deployed — combining AI speed with human oversight.
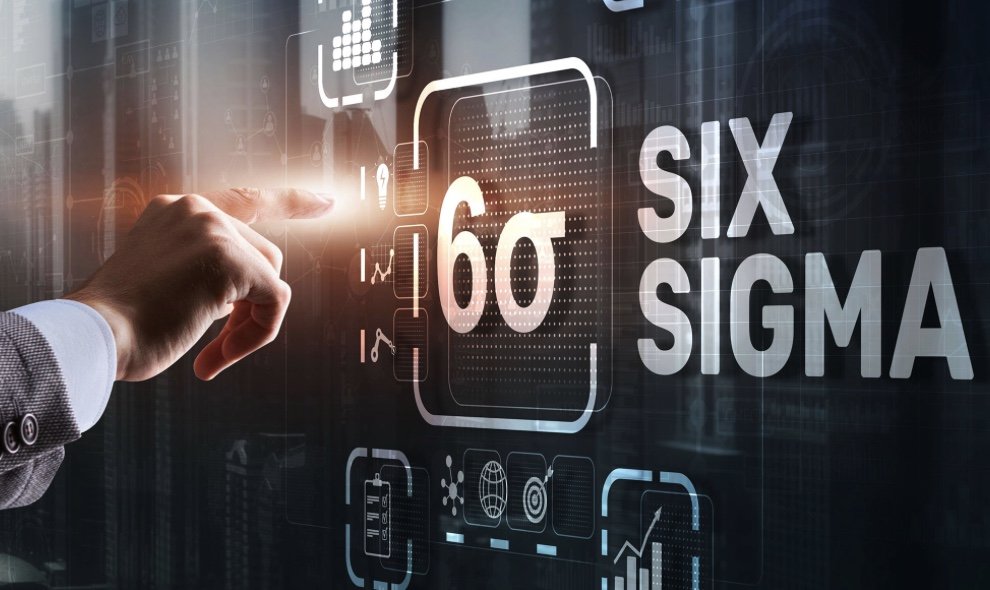
“Quality in a service or product is not what you put into it. It is what the client or customer gets out of it.”